Understanding the Role of a Plastic Injection Mold Manufacturer
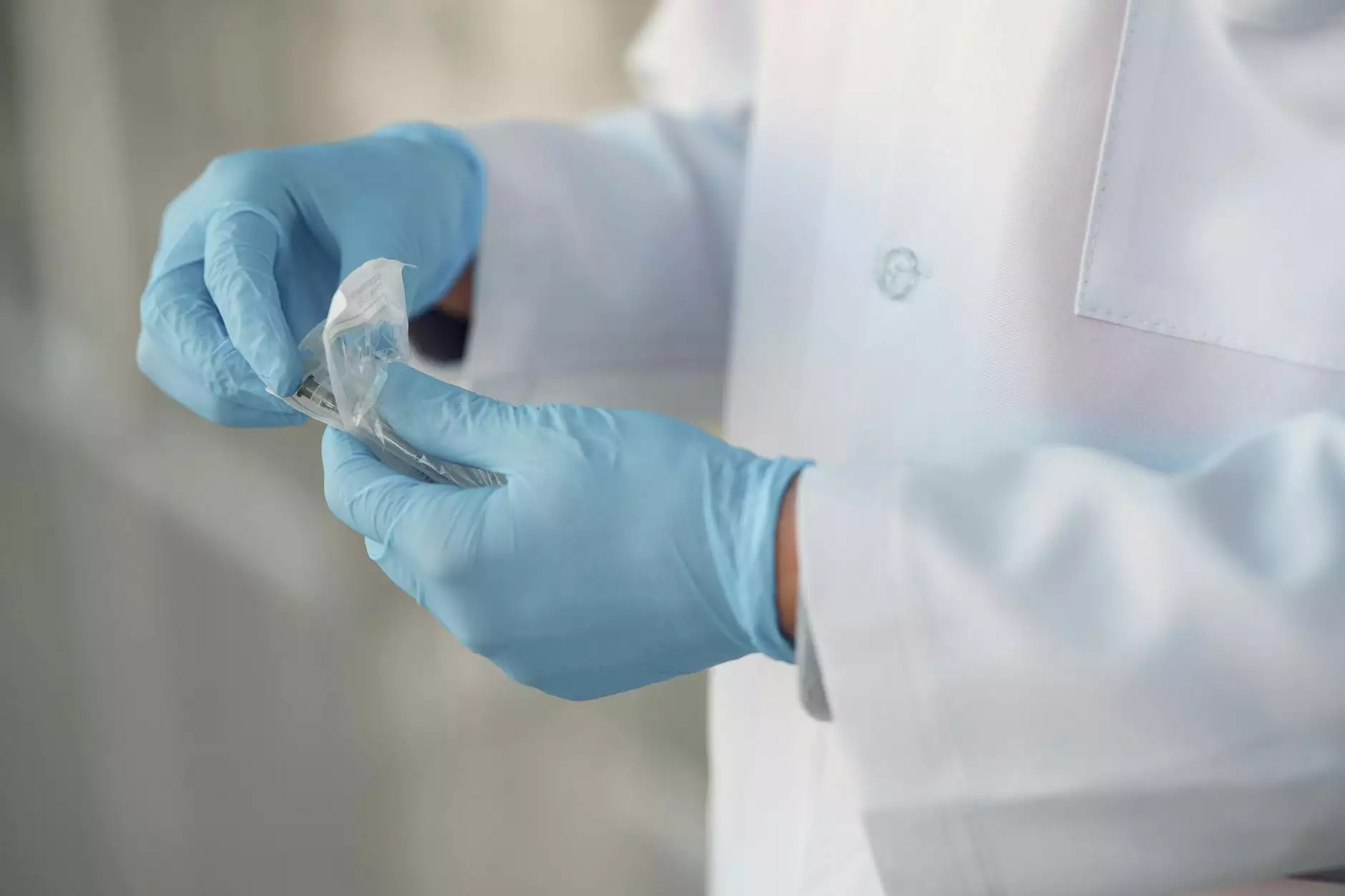
The landscape of manufacturing is continually evolving, and within this dynamic ecosystem, the role of a plastic injection mold manufacturer is paramount. This industry plays a vital part in producing a broad spectrum of products, from simple household items to complex automotive parts. At the forefront of this innovation is DeepMould.net, a premier name in the field known for its dedication to quality, precision, and customer satisfaction.
What is Plastic Injection Molding?
At its core, plastic injection molding is a manufacturing process that involves transforming plastic material into specific shapes by injecting molten plastic into molds. This method offers numerous advantages, including:
- High Production Efficiency: Once the molds are created, numerous items can be produced in a relatively short time.
- Precision and Consistency: Injection molding provides high levels of accuracy and uniformity, ensuring that each product meets exact specifications.
- Material Versatility: A wide range of plastics can be used, making it suitable for various applications across different industries.
The Importance of Choosing the Right Manufacturer
When venturing into plastic manufacturing, selecting the right plastic injection mold manufacturer is crucial to the success of any project. Here are several factors to consider:
Experience and Expertise
The experience of a manufacturer can significantly influence the quality of the final product. Companies like DeepMould boast years of experience across diverse sectors. Their expert teams not only understand the technical aspects of the manufacturing process, but they also keep abreast of the latest advancements in technology.
Customization Capabilities
Every project has unique requirements. A quality manufacturer offers customized solutions tailored to specific needs, whether it involves creating unique mold designs or using particular materials that meet defined performance standards. At DeepMould.net, customization is a key priority.
Technological Advancements
The industry is driven by technological innovation. Companies utilizing the latest technologies in plastic injection molding can provide improved product quality and lead times. For instance, advanced computer-aided design (CAD) software and state-of-the-art machinery enable precision and efficiency that can set manufacturers apart in a competitive market.
The Comprehensive Process of Plastic Injection Molding
The process of plastic injection molding consists of several key stages. Understanding these stages can help clients appreciate the attention to detail that manufacturers like DeepMould put into every project.
1. Designing the Mold
The creation of a mold begins with detailed designs that ensure the final product will be both functional and aesthetically pleasing. This stage typically involves:
- Concept Development: Collaborating with clients to conceptualize the product design.
- 3D Modeling: Using CAD tools to create a precise 3D model of the mold.
- Prototype Testing: Sometimes producing a prototype to test the design before full-scale production.
2. Mold Fabrication
Fabricating the mold is one of the most critical steps. This involves:
- Material Selection: Choosing the right materials (often steel or aluminum) that can withstand the injection process.
- Machining: Employing CNC machining and other manufacturing processes to create the mold.
- Quality Assurance: Regular checks and testing to ensure the mold meets stringent quality standards.
3. Injection Process
The actual injection process is where the magic happens. It involves:
- Heating: The selected plastic is heated until it becomes molten.
- Injection: The molten plastic is injected into the prepared mold.
- Cooling: Allowing the plastic to cool and solidify into the desired shape.
4. Ejection and Finishing
Once the plastic has cooled, the mold opens, and the finished product is ejected. This stage may also include:
- Trimming and Finishing: Removing excess material and adding any necessary surface finishes.
- Final Quality Checks: Conducting inspections to ensure the product meets all specifications and quality standards.
The Diverse Applications of Plastic Injection Molding
Plastic injection molding serves a wide variety of industries. Some of the most notable applications include:
- Consumer Goods: Manufacturing everyday products such as containers, toys, and electronics casings.
- Automotive Parts: Creating components such as dashboards, light housings, and interior fittings.
- Medical Devices: Producing precise components for medical equipment and devices.
- Industrial Equipment: Making parts for machinery, casing, and other industrial applications.
Quality Assurance in Plastic Injection Molding
Quality assurance is a fundamental component of the manufacturing process. For reputable manufacturers like DeepMould, strict quality control measures are put in place to ensure that every product is up to standard. This includes:
- Material Testing: Verifying that all raw materials meet required specifications.
- Mold Testing: Running trials to detect any issues before bulk production begins.
- Final Inspections: Ensuring that every batch meets both client and regulatory standards.
Environmental Considerations in Plastic Manufacturing
With the growing awareness of environmental issues, many manufacturers are adopting eco-friendly practices. A responsible plastic injection mold manufacturer not only focuses on quality but also considers the environmental impact of their operations. This can include:
- Using Recycled Materials: Incorporating recycled plastics into the product range.
- Energy Efficiency: Implementing processes to reduce energy consumption during production.
- Sustainable Practices: Working towards minimizing waste and adopting more sustainable sourcing practices.
The Future of Plastic Injection Molding
The future of plastic injection molding looks promising, with continuous advancements in technology paving the way for even more innovation. Some trends to watch for include:
- Smart Manufacturing: The integration of IoT (Internet of Things) for better monitoring and efficiency.
- 3D Printing Technologies: Combining injection molding with 3D printing for rapid prototyping and production.
- Increased Customization: The demand for personalized products will lead to greater customization in mold design.
Conclusion: Partnering with a Leading Plastic Injection Mold Manufacturer
In conclusion, partnering with a top-tier plastic injection mold manufacturer can be a game-changer for businesses looking to innovate and expand their product offerings. With companies like DeepMould.net, you can expect exceptional service, unparalleled quality, and cutting-edge solutions that drive success in a competitive marketplace.
If you are ready to elevate your manufacturing capabilities and explore the vast potential of plastic injection molding, consider reaching out to a specialized manufacturer today. Your idea could be the next big thing, and with the right partner, it can become a reality.