Precise Injection Molding: Transforming Manufacturing with Accuracy
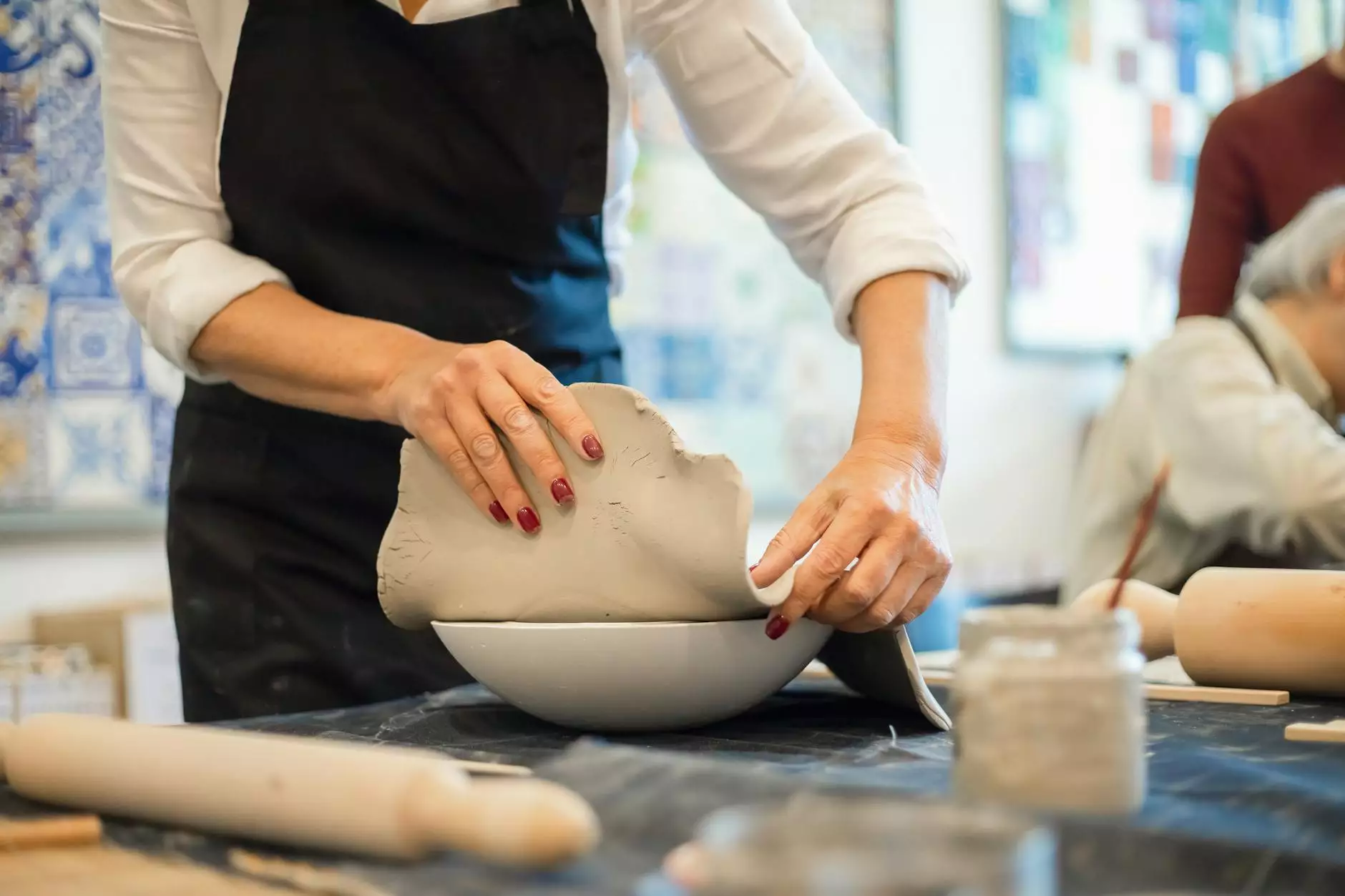
Injection molding has revolutionized the manufacturing industry, providing high-precision and high-volume production solutions. One of the predominant methods utilized by metal fabricators and manufacturers alike is precise injection molding. This technique stands out for its capability to produce complex shapes with extraordinary accuracy, making it indispensable in various applications. In this article, we will delve deeply into the intricacies of precise injection molding, exploring its applications, advantages, and the innovative future it promises.
What is Precise Injection Molding?
Precise injection molding is a manufacturing process used to create parts by injecting molten material into a mold. The materials commonly used include various types of plastics and metals, depending on the application and final product requirements. The process involves several critical steps: material preparation, heating, injection, cooling, and ejection.
How Does Precise Injection Molding Work?
1. Material Preparation
The first step in the injection molding process is to prepare the raw material. This involves selecting the appropriate thermoplastic or thermoset materials and ensuring they are free of contaminants.
2. Heating and Injection
Once prepared, the material is fed into a heated barrel, where it is melted down. During this stage, precise temperature control is essential to ensure that the material reaches the correct viscosity for injection. The molten material is then injected into a mold under high pressure, which allows for detailed shapes and designs.
3. Cooling and Ejection
After injection, the material cools and solidifies within the mold. The cooling time varies based on material type and part geometry. Once sufficiently cooled, the mold opens, and the finished part is ejected, ready for the next steps, such as trimming, finishing, or assembly.
Applications of Precise Injection Molding
Precise injection molding is utilized across a variety of industries. Here are some key sectors where this manufacturing process plays an essential role:
- Automotive Industry: Components like dashboard panels, exterior body parts, and intricate interior features are produced with precision.
- Consumer Electronics: Mobile phone casings, electronic housings, and intricate connectors have transformed with the help of precise injection molding.
- Medical Devices: Critical parts for syringes, inhalers, and other medical equipment demand high accuracy and reliability.
- Packaging: The food and beverage sector benefits from precise and hygienic packaging solutions, which are easily produced through injection molding.
- Industrial Equipment: Components for machinery and industrial applications often require robust yet precise molding solutions.
Benefits of Precise Injection Molding
The advantages of utilizing precise injection molding are numerous. Here’s a closer look at some of the primary benefits:
1. High Reproducibility
One of the standout features of precise injection molding is its ability to produce large volumes of identical parts with minimal deviation. This level of reproducibility is vital for industries that demand consistency and quality assurance.
2. Cost Efficiency
Over time, the initial investment in molding tools pays off as the cost per unit decreases with mass production. Less material waste during the process contributes to cost savings, making precise injection molding a financially savvy choice.
3. Complex Geometries
The ability to create complex shapes with intricate details is one of the primary advantages of this molding technique. The design flexibility allows engineers to innovate without worrying about manufacturability constraints.
4. Material Versatility
Precise injection molding can accommodate a diverse range of materials, from reinforced plastics to metals, enabling manufacturers to select the most suitable material for their specific application.
5. Quick Turnaround Times
The speed of the injection molding process allows for rapid production cycles, crucial for maintaining competitive edge in fast-paced markets.
Challenges in Precise Injection Molding
While the benefits are compelling, challenges do exist within the realm of precise injection molding. Addressing these challenges is critical for ongoing improvement in the manufacturing process:
1. Initial Tooling Costs
The design and fabrication of molds can be costly and time-consuming. However, these costs are usually offset by the long-term production efficiency.
2. Design Limitations
Certain design features, such as undercuts or extremely thin walls, can be challenging to mold accurately, necessitating careful planning during the product design phase.
3. Processing Parameters
Accurate control of temperature, pressure, and cooling rates is crucial. Any deviation can lead to defects in the finished product. Continuous monitoring of these parameters is essential.
The Future of Precise Injection Molding
As technology evolves, so does the landscape of precise injection molding. Innovations such as advanced robotics, AI-driven quality control, and improvements in materials science are shaping the future:
1. Automation and Robotics
Increased automation is optimizing the injection molding process, leading to enhanced efficiency, reduced labor costs, and improved consistency in production.
2. Sustainability and Eco-Friendly Materials
With a growing emphasis on sustainability, manufacturers are now exploring biodegradable and recycled materials for injection molding. This shift reflects an industry-wide commitment to reduce environmental impact.
3. Advancements in 3D Printing
The integration of 3D printing technologies with injection molding is opening new avenues for rapid prototyping and custom manufacturing, thus accelerating product development cycles.
Choosing the Right Partner for Precise Injection Molding
When selecting a manufacturing partner, such as deepmould.net, for precise injection molding, consider the following key factors:
- Experience and Expertise: Look for companies with a proven track record in the specific applications you require.
- Technology and Equipment: Ensure that your partner utilizes state-of-the-art machinery that guarantees product quality.
- Material Knowledge: A strong understanding of various materials and their properties will be crucial for selecting the right one for your application.
- Quality Assurance: Evaluate their quality control processes to ensure they meet your standards.
Conclusion
Precise injection molding is more than just a manufacturing process; it is a critical enabler of innovation and efficiency across multiple industries. As manufacturers increasingly rely on this technique to bring their ideas to fruition, understanding its mechanics, benefits, and future potential becomes vital for any business in the sector. By leveraging the advantages of precise injection molding, companies can not only enhance their production capabilities but also drive forward the next wave of technological advancement. For businesses looking to innovate and optimize, embracing this method represents an essential step into a successful and sustainable future.